By Tom Stelmack, Class of 2017
Editor’s note: To reach the photo album and all the illustration figures noted in the article, CLICK HERE.
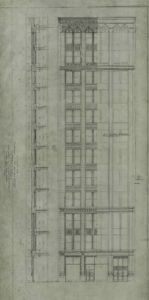
The historic Atlantic Bank building at 168 N. Michigan Avenue 1 now has a new lease on life. It will be adapted and transformed into the Hotel Julian, named in honor of St. Julian, the patron Saint of Hospitality and Travelers. Although the upscale hotel will compete with other boutique hotels in the area, it is expected to succeed, as tourism has reached a new high level in Chicago in 2017; with some trepidation 2 it will continue to grow. The owners and developers are Oxford Capital Group and Quadrum Global. The former is a local investment group that has successfully introduced a total of 12 hotels into this market, some with Quadrum. These include 3: the LondonHouse, Godfrey, Felix, Langham, Hyatt Mag Mile, and Essex Hotel and Tower. Asked why they wanted to develop this property, the response 4 from John W. Rutledge, founder and president of Oxford Capital Group, was, “We continue to believe in the attractiveness and irreplaceability of prime Michigan Avenue real estate and the growing momentum of the areas adjacent to Millennium Park and Grant Park”.
After you read the challenges presented for this project, you’ll fully appreciate their $95m ($75m renovation + $20m purchase) 5 investment and commitment to the area of Michigan Avenue between Mag Mile and Millennium Park. This will be a wonderful adaptive reuse of an historic building in a long-forgotten segment of Michigan Avenue. With the renovation, the 70,400 sq. ft. 12-story building will now be 19 stories and will include a penthouse and a roof-top venue.
The firm of Marshall & Fox designed the 101 year-old Atlantic Bank Building in 1911, with construction completed in 1916. The architectural plans (Figure 1) indicate that the Federal Life Insurance Company commissioned the project. However, Figure 2 shows a view from what seems to be raw space for the office of the President of Federal Life Insurance Company as posted on their website 6 and dated 1912. (It seems unusual that the interior construction would last four years.)
Benjamin Marshall and Charles Fox designed other important structures in Chicago, including the Steger Building (east Jackson); the Drake, Blackstone, and Edgewater Beach Hotels, Sheridan and Lakeshore Trust & Savings Banks, many of the buildings of the South Shore Country Club (the landmarked Clubhouse is now the South Shore Cultural Center) and many homes on the North Shore.
The Atlantic’s east and west curtain walls were terra-cotta, supplied by the Northwestern Terra Cotta Company. Having demonstrated its fire proofing value, the firm dominated the Chicago market. The original lobby sported marble with mahogany paneling. Now only one section of marble remains, and it is in such poor condition that it can’t be used.
When the building first opened, the Federal Life, Insurance Company occupied the upper 10 floors. In the mid-20th century, Maremont 7 (auto parts e.g. catalytic converters) owned the building and established their headquarters there. Maremont sold it in the 1970’s and moved to the Standard Oil Building (AON Center). At one point, circa 1926 8 when the Greek National Bank entered the Chicago market, their Atlantic Bank Division occupied the lower floors. After the bank departed the building 9 in 2009, the original Atlantic Bank sign went missing.

After laying vacant, Crown Commercial Real Estate/Development purchased the building for $7.25m in 2012. Crown had difficulty obtaining approval for a hotel from the Chicago Plan Commission 10. The city’s hotel room window requirement 11 was made difficult to comply with by the building to the south at 150 N. Michigan, the Crain Communications Building. The Toronto-based Hartford Real-Estate Investment owns 150 N. Michigan as well as the gangway space between the two (Figure 3). The city wanted assurance that the owners of 150 N. Michigan would not build in the narrow space which would cut off light and air to the hotel rooms!
Hartford Real Estate was concerned about damage to their building during construction as well as potential fire damage from 168 N. Michigan. Consequently, renovation work stopped but only after many tiles and windows had been removed. The building subsequently became a blight on Michigan Ave (Figure 4).
Crown eventually negotiated an easement with Hartford Real Estate, but then sold the building to Oxford in 2014 for $20m 12. Oxford assumed control in late 2015 with re-approval from the Chicago Plan Commission 13 & 14. The program included demolishing the fragile 15’ cornice, (it is being replaced) and adding six stories (including a penthouse) and rooftop patio. Following a structural analysis by TRGWA which included caisson ‘sounding’, Howard Hirsch and Associates designed the upper floors. The analysis of the twenty-six 6’4” diameter steel-encased caissons that extend 70’ 9” below grade confirmed support for the added load of the additional floors. The glass curtain wall will then extend from the top to the base, through the terra cotta facade (Figure 5). Boston Valley Terra Cotta manufactured the replacement facade tile 15 with restoration provided by Central Restoration. The Gettys Group designed the hotel rooms 16.
More to the story
There is much more to the story of this restoration. The years of abandonment presented significant challenges to the contractor, WE O’Neill. On-site interviews with the Project Manager, Joe Kadow, Project Engineer, Mike Gabel, and Project Supervisor, Pat Kerrigan, revealed these challenges. It is not an easy task to comply with codes that are now quite different from those in 1911. Space confinements and restrictions for the use of heavy equipment were also challenging. I sent several questions about the building’s history and renovation plan to Joe prior to my visit, to which he and Mike provided in depth responses.
I arrived at the rear (west façade) of 168 N. Michigan, which was the main entry during construction. There is access from Wabash Avenue through a parking lot and adjacent to the old Michigan Avenue National Bank drive-in windows (Figures 6 & 9). Obviously it would be quite impractical to work from the Michigan Avenue side.
The ugly old fire escape (Figure 7) had been removed and the terra-cotta tiles already repaired where fasteners were bolted (Figure 8). Here is where I met Joe and Mike and donned my hard hat. A good portion of the lower back wall had been removed to allow construction materials and equipment to be delivered. This area will become an additional lobby entrance on the west side of the building to facilitate vehicular pick-up and drop-off. As we approached the elevators to meet Pat, exposed columns were apparent. The old bank vault had been removed by the prior contractor, Rosewood Commercial 17, leaving a five ft.-thick concrete slab. This was partially removed to afford the plumbing (pipe underdrain system) to be installed under the basement floor.
The building’s original beam and column fireproofing was what you would expect— clay tile brick and blocks. It is now replaced with modern fireproofing (Figure 10). The freight elevator took us up to the 5th floor where evidence of erosion from the prior contractor’s abandoned work became apparent. Clay tiled flooring was often used just prior to this period and was evident (Figures 10 & 11). It was light- weight but eventually fell out of favor with the advent of concrete flooring as noted by historian Tom Leslie 18. Concrete, however, had been used to level the terra-cotta tiles and allow for the nailing of wooden floors, presenting a challenge for renovation. To expose the top of the columns that now required added reinforcement using kicker braces (Figure 11), an area of this terra-cotta tile decking was removed. Because these were continuous long hollow tubes of terra cotta tile supported at each end, removing a cut-out weakened the entire floor. Consequently, a special technique was used to support the flooring as a section was removed. A down-turn beam was created with poured concrete that locked in the clay tile flooring.
Adding to the challenge, the prior contractor left the central column opening and with the poor maintenance of the original roof, rain water drained down through these square cutouts leaving several inches of water in the basement. The exposed steel showed significant corrosive oxidation with flaking, After testing for web and flange section loss, it was clear that the structural integrity had been compromised. The majority of the roof steel required replacement. The method of delivering the steel I beams and securing them was a challenge. I’ll keep you in suspense for a while because there are other beams that must be added.
The building is 45 feet wide, now surrounded to the south by taller structures, to the north by a lower building, and partially exposed to the east and west. However, there was no core, lateral or wind bracing incorporated into the design. At the time of initial construction (Figure 2) it was completely exposed both from the east and south and possibly also from the north. The L train along Wabash partially blocked west exposure. It seems odd that it passed building inspections. However, there are current requirements for these supportive elements. So how does a contractor provide internal bracing not only from an engineering perspective but also logistically?
Engineering and bracing
Let’s start with engineering the supplemental core, lateral and wind bracing. Two systems were used. Each column beam junction was reinforced using a kicker brace plate. However at the upper floors, and to support the added seven stories, additional steel kicker bracing was necessary (Figure 11) as noted by the double angled plates. The building’s central columns were about ½ inch off but toward the south wall the discrepancy became 2 ½ inches, occurring either from settling or poor construction. Here these larger plates connecting beams and columns were needed, especially with the addition of six floors plus the seventh story roof deck. The second system involved supplying a core, which the building didn’t have! So internal “K” cross bracing was needed; think Hancock Building but internally. This was added to what will become the new elevator shafts (Figure 12) and stairwell. The core and fire suppression obviate the need for the external fire escape.
The newly-poured concrete floors also add stability to the steel infrastructure. As noted, there were steel columns and beams whose corrosion was so significant that they required complete replacement. Notably the beams that supported the cornices were unstable (Figure 13). They, along with the cornices, were removed, and both beam and cornice are being replaced (Figure 14). Kudos to the developer and contractor to save an elegant element of this historic building as laid out in the original plans (Figure 15). So if this wasn’t an engineer’s and developer’s challenge (nightmare maybe?!), you’ll see the added logistic challenge of adding the bracing, columns, and beams.
First however, let’s fix the leaky roof before all of the internal renovation becomes compromised. The original roof atop the 12th floor was clay tile and pitched … ready for this? Pitching was accomplished using a buildup of coal cinders three feet thick at the east end and gradually reduced to allow runoff to the west. A new concrete roof was installed, pitched centrally to a drainage system. Eventually this will be replaced after the final roof of the seven-story addition has been completed.
Logistics, muscles and motors
Now for the logistics challenge. Keep in mind that access from Michigan Avenue was not permitted, and the western access was narrow (Figures 6 & 7). Because the city had no data for the weight the parking lots and alley could support, crane rental, which would have made a difficult project easier, was not an option. Fortunately, the Project Supervisor has had much experience working with confined areas. He provided a long list of important buildings in his repertoire. His solution was to bring all of the structural steel elements inside and, using a combination of spider crane and gantry mounted on top of the roof (Figures 16 & 17) , hauled steel beams/columns up through what will become the new elevator shaft (Figure 18). And this included the material needed for cross bracing the shaft itself.
Muscle and motors provided the lifting power, but the process was costly ($2m change orders already) and added six months to the project. The crane/gantry unit was itself raised as the new steel skeleton was being constructed (Figure 19). Added to this logistical challenge was the demolition company that started on the upper floors, using gravity to discard waste. Much of the structural work, then, started on the upper floors and moved downward, in reverse of what normally would occur.
The old steel beams (Figure 20) had been made at the Lackawanna Steel Company plant 19 on Lake Erie near Buffalo; the replacement steel beams and columns are rolled from plants in Indiana and Arkansas. Glazing comes from two companies. Plate glass forming the south curtain wall is made by Quaker (Figure 21) and will be fixed, as is the north wall. The west wall will be double-hung sashes, also from Quaker. The east side, most visible from Michigan Avenue and Millennium Park, will have a continuous curtain wall from the new floors and extending down through the terra-cotta of the original 12 stories, and will feature windows that open (Figure 5). These angled windows are supplied by Wausau. Additionally, the masonry of the south wall had been painted with a non-breathable paint that retained water and created damage (Figure 22). That wall has been fully tuck-pointed.
Earlier I noted that re-approval and negotiations with 150 N. Michigan involved an agreement to leave the gangway airspace open and also to fireproof 168 N. Michigan. A modified sprinkler system will provide another type of curtain wall, a solid sheet of water positioned just behind the south windows to extinguish any fire and prevent it from extending to the 150 building (Figure 21). The design involved some modified engineering for its placement.
Ah! So now what will become of the terra-cotta curtain walls that drape the east and west sides? The 11, 000 pieces of old terra-cotta supplied by Northwestern Terra Cotta were fastened to the columns and mullions using iron but later changed to galvanized fasteners. “Z” fasteners (Figure 23) will now be used for the 1,000 replacement pieces as well as the 1,400 new pieces added on the 1st & 2nd floors of the east façade. The framing required reinforcement with 2 x 10 wood boards bolted to the steel-centered piers and mullions (Figure 24). This is necessary to support the folding glass pattern that will extend from the additional floors to the base (Figure 5). Central Restoration, previously contracted by Musa Tadros of Crown Commercial Real Estate/Development, had already removed much of the damaged terra-cotta and some of the cornice, and Boston Valley Terra Cotta is replicating the tiles and cornice. However, the work has been far more complicated and costly; now with a $2.9m façade restoration price compared to the initial contract of $1.9m. Figure 25 shows examples of the old tiles with newly molded and fired replicas immediately adjacent.
The lobby doors were originally designed to be two stories in height (Figure 26). However the current design specifies that each will be a single story. This modification will add about 10 hotel rooms. A New York firm, Workshop APD, designed the ground floor lobby and restaurant areas. W. E. O’Neil will construct the buildout. As of this writing, the new chef-focused restaurant (Figure 27) will carry the name of “About Last Knife” 20. The Gettys Group is designing the 218+ hotel rooms. European in-wall slim tank toilets along with showers (no tubs) will hallmark these efficient bathrooms. The rooms are described as modern but elegant (Figures 29 a-d).
Needless to say, the southeast views will be spectacular. Compare the current view from what was the 12th floor Presidential Suite for Federal Life (Figure 28) to the 1912 view (Figure 2).
The end is in sight
The current completion date for hotel and restaurant to open is September 2018. I, for one, anxiously await its completion. No doubt the adaptive reuse of this Chicago Commercial style historic building, with its neo-Gothic accents and the Modern flair of its new glass curtain wall, will add character to the Millennium Mile. Of course with St. Julian watching over, it will be a comfortable hotel for its guests.
Special thanks to John Russell, my neighbor and President of W.E. O’Neil Construction. He arranged for me to interview his team for the Hotel Julian project. Joe Kadow, Mike Gabel, and Pat Kerrigan were very helpful to me as I researched this article. I found their solutions to a complex renovation project ingenious.
Editor’s note: To reach the photo album and the illustration figures for this article, CLICK HERE.
Sources:
- located at its original assigned address of 87 – 89 N Michigan Ave on Block 10 lots 17 & 18 of the Fort Dearborn Addition to Chicago
- http://www.chicagotribune.com/business/ct-millenniun-park-hotel-redevelopment-0512-biz-20160511-story.html
- View The Current Newsletter (https://www.hotel-online.com/?ACT=27&ad_id=82) Hotel-Online (https://www.hotel-online.com/) » News (https://www.hotel-online.com/press_releases) » Oxford Capital Group & Quadrum Global Converting Chicago’s Former Atlantic Bank Building into Hotel Julian, Oxford’s Flagship Property
- http://www.ohrllc.com/business-2/coming-soon-hotel-168-north-michigan-avenue/
- https://chicago.curbed.com/2017/4/18/15339200/chicago-development-hotel-julian-michigan-avenue-millennium-park
- http://www.federallife.com/company-history/
- http://www.chicagoarchitecture.info/Printer.php?ID=1342756939
- Handbook on the History of European Banks, section on Greece page 524.
- https://ww.chicagoarchitecture.org/2009/08/07atlantic-bank-building-needs-a-new-name-2/
- http://www.chicagobusiness.com/realestate/20150225/CRED03/150229915/hotel-near-millennium-park-stalled-amid-permitting-snafu 1/
- code 13-172-060 Light and ventilation required
- https://www.bisnow.com/chicago/news/hotel/oxford-capital-wants-to-rase-height-of-michigan-avenue-hotel-project-62486
- https://buildingupchicago.com/tag/168-n-michigan/
- https://chicago.curbed.com/2016/8/29/12695512/chicago-loop-michigan-avenue-hotel-addition
- http://bostonvalley.com/category/168-michigan-avenue/
- http://www.rejournals.com/Articles/2017/04/atlantic-bank-building-on-michig
- http://markdunnett.companybulletin.com/mark-dunnett-oversees-demolition-of-famous-atlantic-bank-building-in-chicago/
- Chicago Skyscrapers. Leslie, T Ch 6 P 104 “Chicago began to accept concrete floors in lieu of terra-cotta between 1903 – 1910.
- Controversially in 1922 became part of Bethlehem Steel; itself now bankrupt
- https://chicago.curbed.com/2017/4/18/15339200/chicago-development-hotel-julian-michigan-avenue-millennium-park
Wonderful article! Pris
Thank you – very interesting!
Thanks, Tom, for your work on this article. Amazing preservation/reconstruction story. David Matenaer